|
设备的智能化运维是使用大数据、人工智能技术等相关技术,将传统的设备运维赋予智能的实践。目前可以见到的概念、提法可谓是“乱花渐欲迷人眼”。但是,工业人对设备智能运维的总体感觉总是“理想太丰满,现实很骨感”,很多经历过项目的人都在困扰数字化、智能化运维如何落地的问题。
在上期的文章中,我们对设备智能运维的一些基本概念进行了梳理,而下面将要讲述的落地方法也将以那些正确的设备智能运维概念为基础。
设备智能运维的落地大致可以分为如下图所示的7个基本步骤:
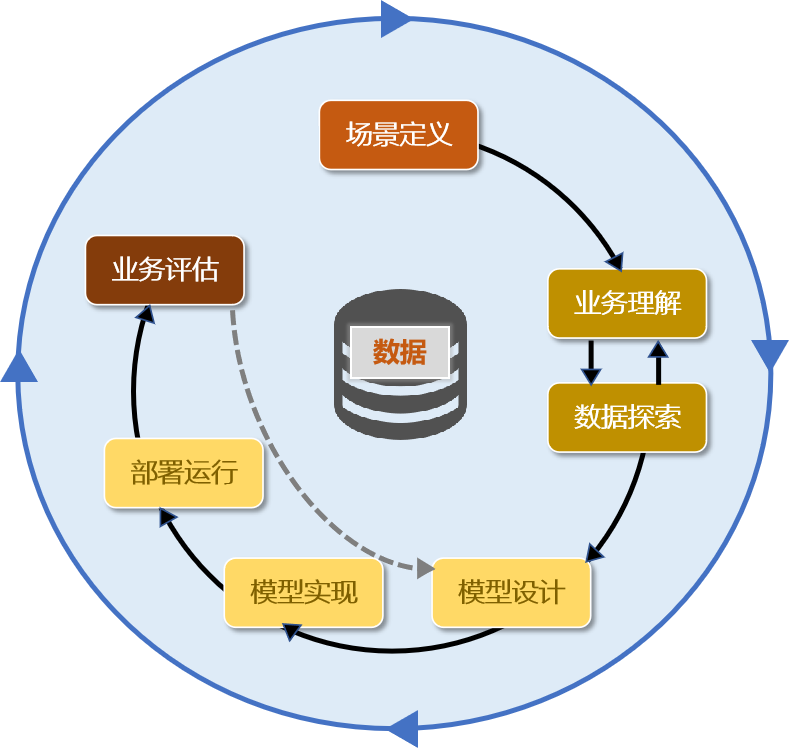
这7个步骤是通用的设备智能运维的实施步骤,但7个步骤并非一次性的线性路径,实践中需要将设备智能运维的大话题进行一定的拆分,界定出场景明确、价值清楚的小问题,并在小问题的执行迭代中不断完善,同时进行横向扩展,逐步实现工业企业的设备智能运维的总体目标。不难看出,设备智能运维的总体落地思想是从一个点开始,从点到面的扩展则分为两个维度:纵向扩展:具体问题(点),经过7个步骤的反复迭代,使提升智能运维效果,提炼实现的具体可行方法不断优化,提升。
横向扩展:从一个点开始,通过通用的方法论横向对相似的设备进行复用改造,逐级扩展,直至全域覆盖。
具体落地步骤
第一、 场景定义
场景定义是在一开始的时候确定“落脚点”的工作。具体而言就是如何确定一个足够SMART的问题,界定其对应的业务价值,并给出对输出结果的正确期待。
不SMART的场景:“我要做智能运维”、“我要提升效率”、“我要降低备品备件库存”、“我要软件替代人”。
SMART的场景:“空气压缩机机械系统振动状态的评估”、“以汽轮机级组效率为目标的汽轮机状态评估”、“风力发电机主轴系统振动状态异常识别”、“水轮机主轴轴心轨迹异常识别”、“汽车生产线升降机构系统状态评估(机械系统)”工业企业中设备的组织运行方式有很多种。其中一种比较典型的是围绕高价值单体核心设备展开的运维。例如水电站、风力发电机、大型空压机等 。这些情况下对核心设备机组的要求高,关注多,分析手段丰富;另一方面设备的维护保养工作也比较复杂,需要提前计划安排。因此,这种场合下的设备后续运维分析方法和手段具有一定的深度。
另一种是工厂车间里生产线形式的设备组织形式。例如电路板生产线设备、汽车生产线的众多生产设备等。这种生产线并非围绕某个核心设备展开的,但是作为一个流程中的环节,某个设备引起的生产流中断,依然可能会带来较大的停机损失。有时候这些设备本身的价值与停机损失比是很小的,维护保养工作也不算复杂,但对生产造成的影响仍然很大。这样的设备群组运维方法和分析手段与核心设备是不同的。
场景定义也包含对项目预期的确定。一些不切和实际的运维期望也是设备智能运维项目无法得到良好结果的重要因素。
电机到底该怎么维护?
在核心设备是电机本身的情况下(例如水电站的发电机),电机是核心维护目标,电机单体价值占整个设备的比例大,因此电机本身使用的测点相当丰富,包括各个绕组的温度、电流、轴承振动、轴承温度、润滑油量、润滑油压……,可以说对电机的监测和维护可以细节到零部件级别。
例如:水轮发电机绕组温度分布分析;机组轴承冷却系统油温监控与分析;推力轴承温度分析;导轴承温度分析;发电机润滑系统油压监控与分析……
以上所有的课题和测点都是一台电机里的某个部分,将一台电机的健康拆解为各个零部件的健康。
对于生产线中的电机而言,比如汽车生产线,一条生产线由几百台小电机构成,但是每台电机都很小,价格低。电机出现故障直接更换电机,设备厂家往往不会维修电机(那样不合算),这种情况下如果对电机进行复杂的监测,安装完备的传感器,有可能传感器价格都超过电机本身价格,因此,这种情况下电机的监测就会比较粗糙,电机本身就被当做一个零部件处理。
上述差异直接影响了电机的测点布置,测点采样要求,分析颗粒度要求,分析深度要求等后续各个步骤的落地步骤。
例如:汽车生产线升降机构电机(组)健康评估,仅仅通过一个振动测点,或者电流测点对整台电机进行评估。可能不添加新的测点,或者仅仅添加一个振动测点的方式进行。评估对象也不仅仅是一台电机,而是一组(数台)小电机。
第二、 业务理解
业务理解在设备智能运维领域包含对设备机理的理解和设备实际管理操作的理解,以便确定最“匹配”业务实际需要的数据分析模型。
在众多数据分析项目中,如果缺乏对工业机理的理解,往往可能通过复杂的手段得出已知的简单机理。有人会笑话“大数据分析半天,分析出了个牛顿第二定律”。这种情况的产生,是分析前沟通不充分造成的,并非数据分析本身的问题。从算法角度讲,设备机理就是所谓的先验信息,而数据分析就是在先验信息基础上,通过一定的算法对实际数据进行处理得到后验信息,以提供用户以基于数据的洞察。而缺乏足够的先验信息,也就很难让算法更匹配当下的问题本身,显然会大幅降低数据分析算法的效率。
业务理解在设备智能运维领域中还包括对设备实际管理、操作、使用的日常方式的理解。正如场景定义里讲到的两大类设备——单体高价值核心设备和产线众多小设备的运维方式截然不同,而数据分析算法的输出是需要结合现实运维的处理手法来匹配。有了这两步工业工程师与数据分析师的共同工作,就很好的定义了要解决的问题:目标、边界、前提和输出。一个好的工作总是从定义一个好问题开始,而以下第3-6步是工业数据分析在设备智能运维领域里的具体工作,也就是如何在一个好问题定义下解决问题的过程,将在下一篇文章单独展开。
第三、数据探索
在业务理解和样例数据上,初步验证机理与数据的对应性,形成数据分析模型的原型;
第四、模型设计
在数据分析模型原型基础上,对数据接入、数据资源化、数据流图、数据应用等几方面进行详细的设计。
第五、模型实现
在完整离线数据基础上,考虑算法和软件的一系列工程化问题(如数据质量问题),开发完整的数据分析模型和应用。
第六、部署运行
考虑模型的业务实际需求,在工业数据分析平台上部署算法,并设定模型相应的运行、调度和维护策略。
第七、业务评估
基于使用者的要求,基于场景定义中合理的分析预期,评估算法模型的工程化执行效果,并进行必要的迭代直至满足项目要求。从业务场景定义开始,到业务价值评估完成一个小闭环。这里的业务评估指的不仅是某个智能运维场景的交付,更是设备使用者在后续使用中对设备数字化和智能化运维的不断迭代和提升。业务评估是下一次出发的起点,而非全部事情的终点。一个真正落地的设备智能运维工作,不是一两个课题就能完成的,也不是一个算法、一个软件能解决的,而是一种运维工作方式的改变,是设备使用者通过智能运维方法提升设备运维效率的反复迭代工作。工业设备林林总总,数量大、种类多,只有工业人在不断使用,实践和修改中迭代前行,才能真的让设备智能运维落地。 |
|